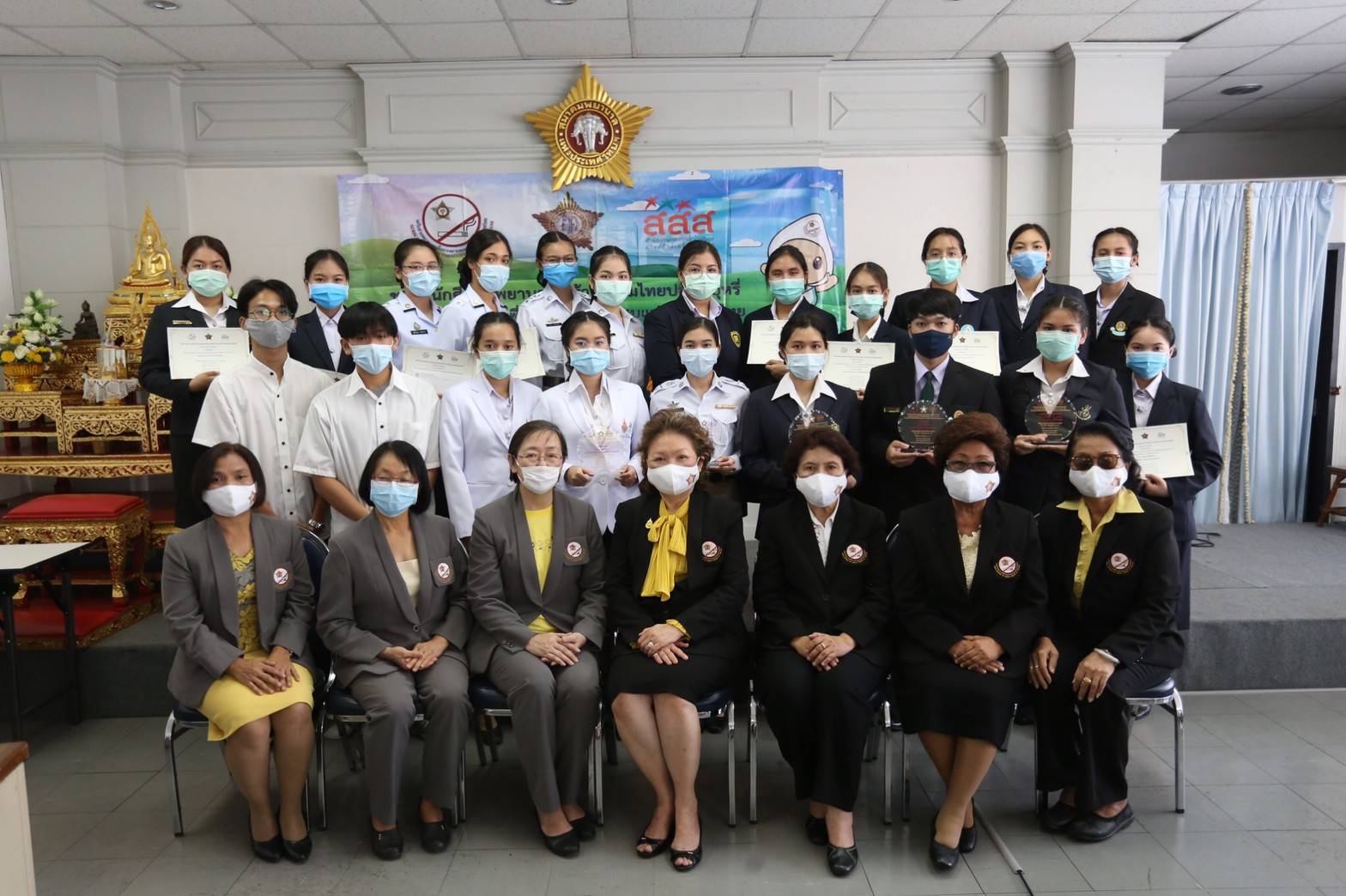
RMUTT pleased to be awarded first prize for “Thailand Cigarette-Free” campaign
25/11/2020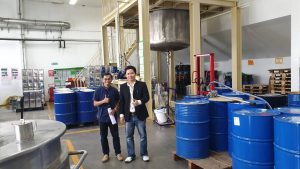
RMUTT researchers driving high potential “Paint Industry Businesses’ towards BOI
26/11/2020RMUTT researcher coverts waste materials into useful products
Another staggering research on “Application of rotational molding method to convert hybrid-plastic waste material into useful products” conducted by Dr. Narongchai O-Chareon, Department of Materials and Metallurgical Engineering, Faculty of Engineering Rajamangala University of Technology Thanyaburi (RMUTT) had financially been supported by the Thailand Research Fund (TRF) with Grand Challenges Thailand initiative for “Area-Based Development Project 2019”. Dr. Narongchai revealed that this experimental research aimed to focus on molding plastic waste materials such as plastic film and plastic bags into useful products using rotational molding method. In the initial stage of the testing, it was found that melting rate, particle size and shape of material particles were considered important factors (very or somewhat) for the rotational molding process. Moreover, the tendency of improving molding ability could be conducted by mixing plastic that suited rotational molding. Concerning the preparation for molding materials and machine, plastic wastes such as plastic bags were used while Single Shaft Shredder machine was specifically designed for lab testing by the Department of Materials and Metallurgical Engineering, Faculty of Engineering, RMUTT. After thorough testing, it was found that the machine could shred tough and thin plastic film outstandingly while blade rotation problem was not found. After finished preparing materials, rotational molding machine called, “Axial Powder flow Apparatus was applied in order to create sample making mold at 190 ° C with 7 rounds of rotational speed per minute, and 2000-watt heating device. Regarding to the internal temperatures found during rotational molding process of the two different plastic materials used including plastic powder of recycle plastic and linear low-density polyethylene (LLDPE), the comparative testing of the materials showed that plastic powder of recycle plastic took more time for molding when compared to the LLDPE in terms of Tack Temperature, Kink Temperature and temperature at which plastic powder changed from (Solid stage) to (Melt stage). Moreover, it was also found that at the stage of structural change, powder was at the complete stage of amorphous phase which could obviously be seen as a form of crystalline color. It is clear from the experiment that recycled film materials took longer to form than the commercial materials, and thus, corresponding to the test results from the melting rate tester. It was found that the melting rate of commercial LLDPE used in the rotational molding industry took significantly less time and temperature than the recycled plastic film powder.
In this research, polyethylene plastics with linear low-density or (LLDPE) powder was mixed with plastic powder of recycle plastic using rotational molding process at ratios of 30, 40 and 50% by weight. The result showed that at the compound rate of 30% (LLDPE 30:70 plastic bags) had the best resistant rate to compression.
It could be said that different types of plastic wastes including plastic bags, plastic bottle caps, plastic containers and plastic gallon could all be molded to create new plastic buckets through rotational molding process. Additionally, the research won its first prize for “Community Solid Waste Management Innovation Product Contest” at “The Local Waste Management Innovation 2019 “event under the campaign of “Reduction of Plastic, Foam and Single Use Plastic” hosted by the Department of Environmental Quality Promotion, Ministry of Natural Resources and Environment Agencies. For those who are interested in the research or needed advices for plastic waste management, please call the department at 091-7758757.