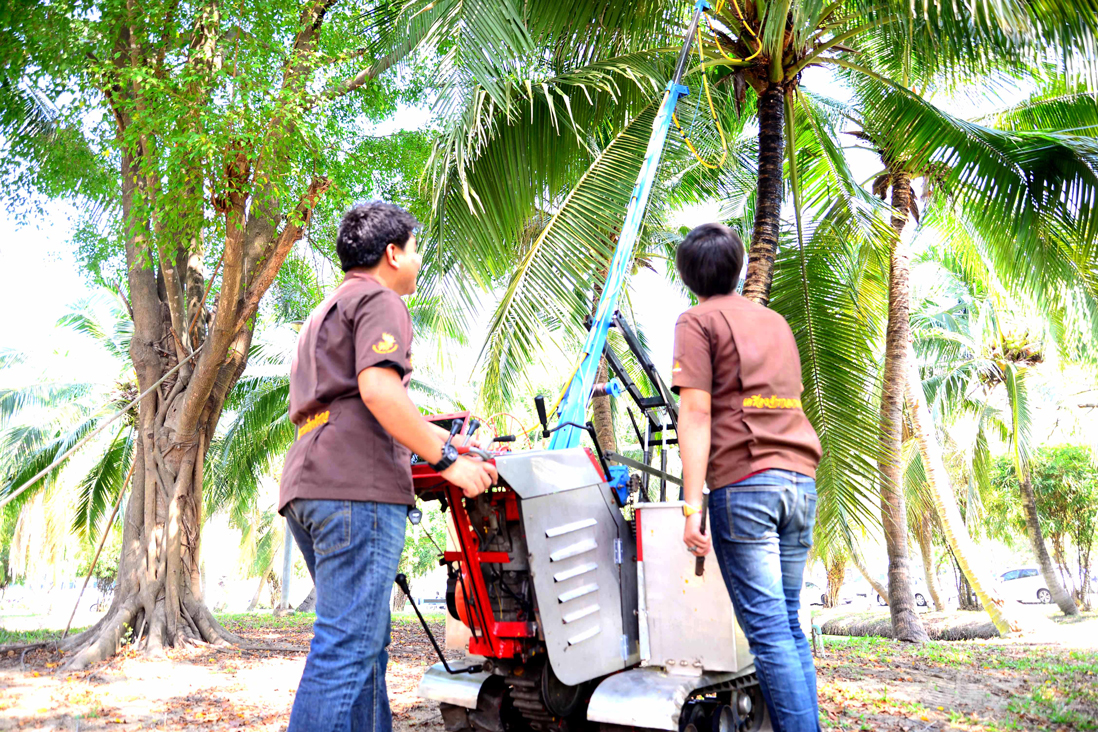
Helping Coconut farmers with a Long Distance Air Spray to Eliminate Pests that feed on Coconut
15/09/2016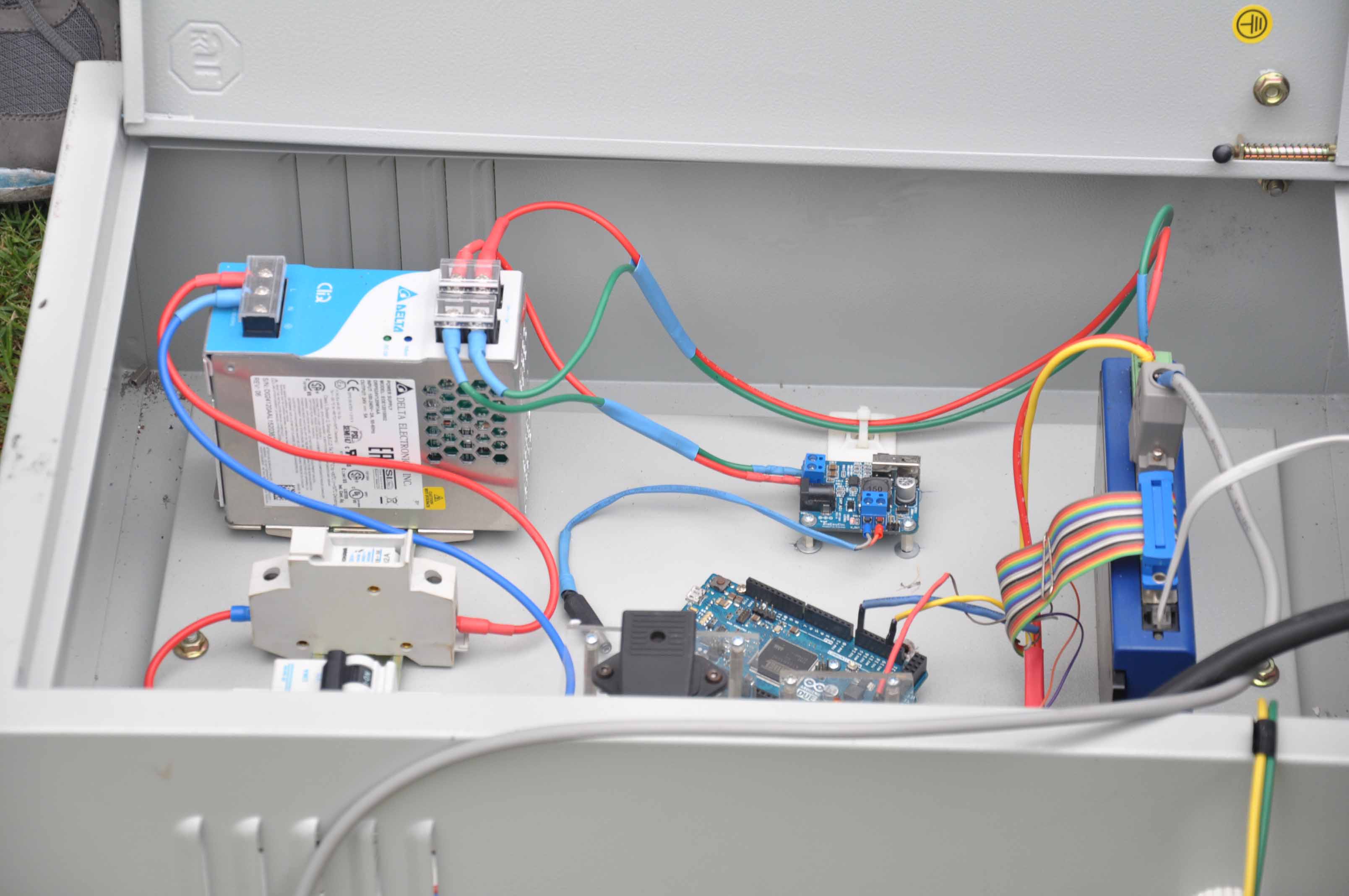
Solar Tracking System for Solar Cell Panels by Using a Micro-controller
15/09/2016Asst. Prof. Dr. Sakorn Chonsakorn and Dr. Rattanaphol Mongkholrattanasit, along with Professor Supanicha Srivorradatpaisan, researcher and permanent professor from the Department of Textiles and Garments, Faculty of Home Economics Technology at RMUTT have developed natural fibers from Water Hyacinth to make creative textile products.
Asst. Prof. Sakorn Chonsakorn said that The Development of Water Hyacinth fiber to Creative Textile Products received research funding from the Thailand Textile Institute to conduct research to extract Water Hyacinth fibers by mechanical means. Professors studied about spinning yarn , fabrics, and textile products from Water Hyacinth fibers. Majorly, there has been development in parallel with finding benefits of using agricultural crops. The textiles industry is considered an industry that supports natural fibers. Furthermore, the guide for development, initiated by The Eight National Research Policy and Strategy (2012-2016), emphasized on building strategic capabilities for economic development. The strategy of this research was to focus on enhancing the effectiveness of agricultural production, which included creating value for agricultural products, forestry, and fisheries.
There are three types of Water Hyacinth, a weed that serves no purpose. The difference between each type is that Water Hyacinth can absorb more organic Nitrogen, at approximately 95%, than other forms of Nitrogen, such as Nitrate Nitrogen, at about 80%, and Ammonia Nitrogen, at about 77%, respectively. The most important finding is that the Water Hyacinth’s trunk consists of a vast amount of long fibers. Thus, professors had an idea to develop natural fibers from Water Hyacinth, in order to produce textile products.
The first step in extracting Water Hyacinth fibers by mechanical means is to source Water Hayacinth from rivers and canals, such as Rangsit canal in Tambon Khlong 6, Thanyaburi district, PathumThani province. Select Water Hyacinth with trunks about 50 cm long, clip it from the canal by extracting the roots, immediately cut the roots and leaves, then tie them together and place them in the same direction so they can be easily transported and kept. Usually, 1 Kg of Water Hyacinth stems or trunks will contain approximately 12-15 trunks. Clean the trunks and tie theme with rope. After that, extract the fibers using a semi-automatic fiber extraction machine by inserting two trunks into the machine each time by using the concept of linear rotation, in order to grate the outer layer of the Water Hyacinth trunk, resulting in long staple fibers, produced from one Water Hyacinth trunk. Next, naturally dry the Water Hyacinth fibers. The chemical composition of Water Hyacinth fibers are as follows: 72.17% cell walls, 52.63% Lignocellulose, 2.25% Lignin, 19.54 Hemicellulose, and 50.38% Cellulose. The fibers are 30-50 cm long and white and cream colored, with a diameter of 50 µm. The surface of the fibers are complex and feels soft when touched. The resolution is 48.55 deniers with a tensile strength of 58.62 g-force per denier, and 7.72% cm elongation before breaking.
The second step is to spin yarn from Water Hyacinth fibers, a natural fiber that has a large lumen, is highly porous, has a high viscosity, and a complex outer surface suitable for retaining air. Output of spinning yarn from Water Hyacinth fibers reveal that the fibers that have completed the process of cleaning with bleach and carding will have an average length of 8.45 cm, an average resolution of 4.52 deniers, an average tensile strength of 9.36 g-force per denier, and an average elongation before breaking of 15.32% cm. In addition, it has slightly bent mark, suitable for open-end spinning. It is necessary to spin yarn mixed with Water Hyacinth fibers and rayon fibers in order to produce yarn that is able to absorb moisture well and is strong.
The ratio of Water Hyacinth fibers and rayon fibers of No. 20 Ne is 20% mixture of Water Hyacinth fibers and rayon fibers, and 80% rayon, while No. 10 Ne is a 40% mixture of Water Hyacinth fibers and rayon fibers, and 60% rayon. Results from physical property tests of Water Hyacith yarn reveal that No. 20:80 has a size of 20 Ne or 33.78 tex while No. 40:60 has a size of 10 Ne or 62.11 tex. In terms of average turns per inch (tpi), the 40:60 yarn has 21 turns per inch. Besides a high tensile strength, the 40:60 yarn has 2.83 Newton strength and 15.17% cm elongation before breaking. In terms of consistency No. 20:80 and 40:80 were inconsistent, gnarled, and uneven. Results from producing fabric and textile products revealed that Water Hyacinth yarn can be used to produce both woven and knitted fabrics with an average thickness of 0.91 mm and an average weight of 302.5 g per square meter.
The third step is to produce fabric and textile products from Water Hyacinth fibers such as using special Water Hyacinth fibers, produced with a Rapier machine, using Water Hyacinth bane yarn 10 Ne. No. 10 Ne yarn can be weaved in special patterns as the blades of the textile machine cut the fabric 60 inches wide, and the special fabric has tensile strength, elongation at break, and tearing resistance.
The fourth step is to design and produce creative textile products, which may include apparel and accessories such as clothing, hats, and shoes. Other products may include home textiles and table linen.
Compared to linen fibers and hemp, the properties of the Water Hyacinth fibers make it lightweight and not hot or stuffy when worn as clothing. Furthermore, weeds that serve no purpose have been applied to add value to the textile industry. Natural fibers have been used to make yarn to produce fabric for creative textile products, which meet the needs of the textile market and is also environmentally friendly. In addition, entrepreneurs, community enterprises, designers, and students can apply technology in creating natural fibers from Water Hyacinth to differentiate their textile products, creating more opportunities for the Thai economy, in order to be the leader of natural fibers in the ASEAN Economic Community (AEC). Those that are interested can ask for more information by contacting Asst. Prof. Dr. Sakorn Chonsakorn from the Faculty of Home Economics Technology or calling 02-5493164.